Camiones Liebherr realizan histórica conexión de trolley en Collahuasi
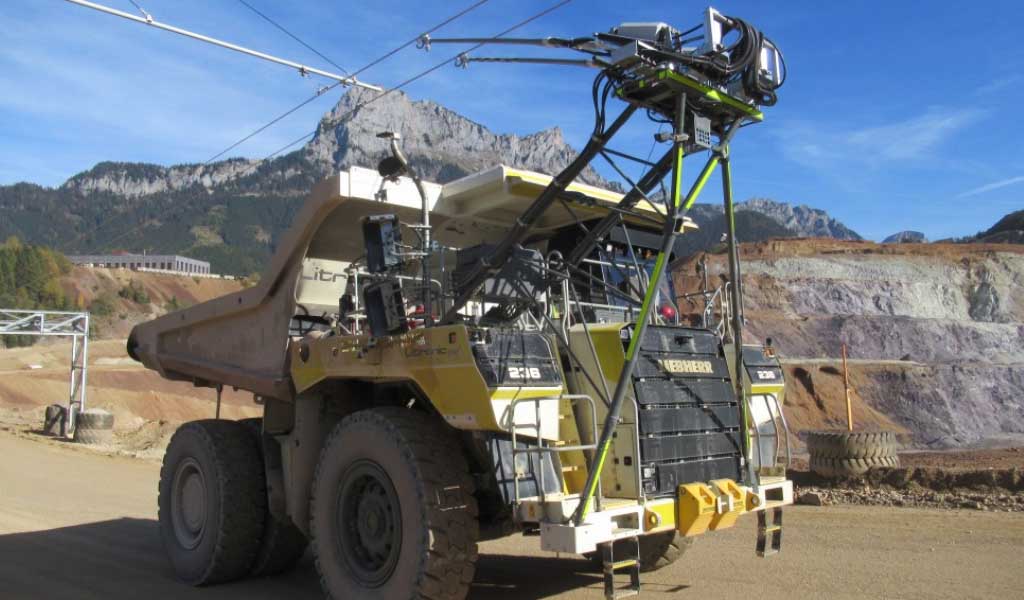
A más de 4.500 m.s.n.m, la chilena Collahuasi es la tercera mina de cobre más grande del mundo y, está allanando rápidamente el camino hacia un futuro más sostenible.
Se ha marcado ambiciosos retos como el Proyecto 210, que aumentará la capacidad de procesamiento de la planta a 210.000 t/d, y el Proyecto C20+, que, a través de una planta desalinizadora, reducirá significativamente el uso de agua dulce en este contexto de evolución y crecimiento.
La innovación orientada a una mayor sustentabilidad también se extiende a su proyecto piloto trolley assist, una colaboración con Liebherr Mining que, según Collahuasi, busca marcar la pauta para la industria nacional haciendo una minería más sustentable y eficiente.
Es el primero de su tipo en Sudamérica, e involucra cuatro camiones Liebherr T 284 clase 400 toneladas en una línea piloto de troles de 1 km. El piloto ya está en marcha y, como tal, los aprendizajes y resultados serán de gran importancia para la industria, tanto para el cobre sudamericano como para el resto del mundo, especialmente para ver cómo funciona un sistema de trole a gran altitud con esta clase de camiones de tamaño superior. En el futuro, estos conocimientos también serán muy valiosos a medida que surjan soluciones relacionadas, como el carro de batería y el carro híbrido.
Manuel Vera, Gerente de Gestión de Activos de Collahuasi: «La idea de este proyecto fue convertir cuatro camiones con tecnología de punta para generar los aprendizajes que nos permitan mirar hacia el futuro y mejorar la sustentabilidad en los proyectos y operaciones...en este tramo electrificado, los camiones irán significativamente más rápido y reducirán en gran medida su consumo de diésel.»
Y añade: "Aquí estamos a 4.700 m, donde tenemos unas condiciones climáticas muy extremas. Tenemos dos inviernos, uno altiplánico en el que tenemos descargas atmosféricas intensas o rayos, con mucha lluvia, y tenemos otro invierno, el continental que estamos viviendo ahora, con temperaturas muy bajas, nieve y hielo a veces. Por lo tanto, el piloto adquiere mayor relevancia porque podremos probar la tecnología en condiciones extremas y generar efectivamente aprendizajes y mejoras."
Los beneficios potenciales son significativos: una drástica reducción en el consumo de diesel, menores emisiones de gases de efecto invernadero y un aumento significativo en la velocidad de ascenso de los camiones.
Carlos Núñez, Vicepresidente de la Mina Collahuasi: "Este piloto nos permitirá verificar todos los beneficios de todos los estudios que hemos realizado: en ahorro de combustible, en reducción de emisiones, en lograr un proceso más seguro, en reducir daños y esfuerzos en los motores de los camiones... estamos haciendo un proyecto en una rampa de subida cargada de 1 km. Con los resultados de este piloto, queremos revisar otras zonas, principalmente en la primera etapa, en los vertederos, que representan las mayores distancias de transporte y, por tanto, las mayores exigencias para nuestros camiones.
La planificación ha sido muy importante porque hay actividades de proyecto de ingeniería, cuestiones eléctricas y otros retos para hacerlo compatible con la operación. Hemos tenido que formar a nuestros operarios".
En la rampa de 1 km, el camión circula casi al doble de velocidad. Eso influye mucho en la eficacia del ciclo". Collahuasi dio una estimación rápida, de unos dos minutos de ahorro por ciclo, lo cual es enorme si se tiene en cuenta el número de ciclos de camión que tiene al día. Para el vertedero, la duración media del ciclo de un vertedero es de entre 48 y 55 minutos.
Sólo el proyecto piloto debería reducir las emisiones de CO2 entre 4.000 y 5.000 t al año. Hoy, Collahuasi está en unas 560.000 a 570.000 t de emisiones de CO2 de Alcance 1. La idea es que este piloto, ojalá, funcione bien y pueda ser escalable en el corto a mediano plazo. La elevación del pantógrafo es automática, aunque el operario todavía tiene que pulsar un botón para engancharlo y también bajarlo al final de la sección del carro.
Oliver Weiss, Vicepresidente Ejecutivo de I+D, Ingeniería y Fabricación de Liebherr: "Nuestra amplia experiencia con soluciones de trolebuses demuestra que las carretillas sobre trolebuses pueden desplazarse hasta 1,8 veces más rápido en comparación con las carretillas diesel, lo que puede traducirse cuesta arriba en una mejora de la productividad del 21%. La experiencia de Liebherr con soluciones de trolebuses abarca más de 50 camiones de 400 toneladas y una flota de camiones de 100 toneladas en la línea de trolebuses más grande del mundo con una distancia de 5 km.
Liebherr Mining inició conversaciones con Collahuasi en 2022, y el sitio presentaba algunos desafíos que debían ser considerados en el diseño e implementación de una línea de trole, todo lo cual era nuestra responsabilidad, ya que habíamos sido contratados para proporcionar la solución completa de trole incluyendo la infraestructura y los camiones mineros a Collahuasi."
Y añade: "Ahora que los camiones están en funcionamiento y el sistema está activo, Collahuasi gestionará el mantenimiento continuo de la línea de carros. Liebherr Mining ya ha impartido formación a los operadores de las carretillas y seguirá prestándoles apoyo para garantizar que las carretillas y la línea de carros puedan aprovecharse al máximo. Este ha sido un proyecto de verdadera colaboración entre Liebherr Mining y Collahuasi; es un testimonio de las asociaciones estratégicas."
Fuente: Tecnología Minera